In industrial flow control, butterfly valves stand out as indispensable tools, offering efficient regulation and control of fluid flow. From their versatile design to widespread applications across various industries, butterfly valves are crucial components in numerous systems. In this comprehensive guide, we’ll delve into what butterfly valves are, their components, the industries they serve, how to use them, their advantages and disadvantages, and factors to consider when choosing one.
What is a Butterfly Valve?
A butterfly valve is a quarter-turn rotational motion valve, typically used to regulate or isolate fluid flow within a pipeline. Its name is derived from the wing-like disc positioned in the center of the valve body, which rotates on a shaft to control flow. When fully open, the disc aligns with the flow direction, minimizing obstruction and pressure drop. A 90-degree rotation completely shuts off the flow, making it a reliable on/off valve.
Components of Butterfly Valves
Butterfly valves consist of several key components:
- Valve Body: The main outer structure of the valve, housing internal components. It connects the valve to the external operating mechanism that drives the disc and to the plumbing system.
- Disc: Also known as the “butterfly,” this disc controls flow by pivoting perpendicular to the flow direction.
- Shaft: The rod that connects the actuator to the disc, facilitating its rotational movement.
- Seat: The sealing surface where the disc makes contact to prevent leakage.
- Actuator: Mechanism responsible for operating the valve (manual, electric, pneumatic, or hydraulic).
Industries Utilizing Butterfly Valves
Butterfly valves find application across a wide array of industries, including:
- Water & Wastewater Treatment: Ideal for controlling flow in water distribution and treatment systems due to their low maintenance and tight shut-off.
- Power Generation: Used in various applications within power plants, including cooling water systems and flue gas desulfurization processes.
- Oil & Gas: Popular for regulating flow in pipelines due to their lightweight design and quick operation.
- Chemical Processing: Employed in various chemical processes due to their resistance to corrosive chemicals and ability to handle slurries.
- Food & Beverage: Widely used in food and beverage production due to their sanitary design, high durability, and ease of cleaning.
- HVAC & Building Automation: Manage airflow in heating, ventilation, and air conditioning systems due to their compact size and quick response.
How to Use Butterfly Valves
Using a butterfly valve involves several steps to ensure proper operation and effective fluid control:
- Ensure that the valve and associated piping system are clean, debris-free, and properly installed according to manufacturer guidelines. Check that the valve is in the fully closed position initially.
- If the valve is equipped with an actuator (manual, pneumatic, electric, or hydraulic), follow the manufacturer’s instructions to power up or engage the actuator.
- During valve operation, monitor system parameters such as flow rate, pressure, and temperature to ensure they remain within safe operating limits.
- Depending on the application, adjust the valve position as needed to achieve the desired flow rate or pressure. For throttling applications, gradually adjust the valve position to control the flow rate within the required range.
- When shutting down the system or if maintenance is required, gradually close the butterfly valve to stop fluid flow. For manual valves, rotate the handle or lever in the opposite direction of opening until the valve is fully closed.
- Regularly inspect the butterfly valve and associated components for signs of wear, corrosion, or damage.
Types of Butterfly Valves
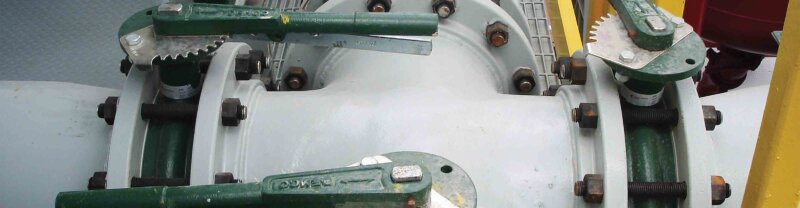
There are several types of butterfly valves, each designed for specific applications and operating conditions. Here are the main types:
- Concentric Valve: Common type with centered stem and disc, suitable for general-purpose applications.
- Double Offset Valve: Features offset stem and seat for tighter sealing, ideal for high-pressure and high-temperature applications.
- Triple Offset Valve: Incorporates three offsets for bubble-tight shut-off, used in critical applications like high-pressure steam and gas.
- Resilient-Seated Valve: Soft-seat design for bubble-tight shut-off, commonly used in water treatment and HVAC systems.
- High-Performance Valve: Designed for demanding applications with metal seats and high-grade materials.
- Lug Style Valve: Features threaded inserts for easy installation between flanges, suitable for frequent maintenance.
- Wafer Style Valve: Compact and lightweight design for easy installation between flanges in tight spaces.
- Flanged Valve: Direct connection to pipelines with flanged ends, available in various pressure classes and sizes.
Advantages of Butterfly Valves
- Cost-Effective: Generally more economical than other types of valves.
- Compact Design: Requires less space, simple mechanism, and lighter weight compared to other valve types.
- Quick Operation: Offers rapid on/off functionality, enhancing process efficiency.
- Minimal Maintenance: Simple construction reduces maintenance needs and costs.
- Versatility: Compatible with a wide range of fluids and applications.
- High Capability: Capable of handling high fluid flows with suspended materials at comparatively low pressures.
Disadvantages of Butterfly Valves
- Limited Pressure Rating: Not suitable for high-pressure applications.
- Throttling Limitations: May not provide precise flow control at partial openings.
- Potential Leakage: Depending on the design, some valves may experience seal wear over time.
- Temperature Constraints: Performance may be compromised at extreme temperatures.
- Cavitation Risk: In certain conditions, cavitation can occur, leading to damage and noise.
How to Choose the Right Butterfly Valve
When selecting a butterfly valve, consider the following factors:
- Application: Define the fluid type, pressure, temperature, and desired flow control.
- Material: Choose body, seat and disc material based on corrosion resistance, fluid type, temperature, and pressure requirements. Butterfly valve is often selected with a cast iron body and a ductile iron disc for general water systems while higher-quality materials like aluminum bronze discs are used for applications in water treatment where the water may contain corrosive chemicals.
- Size and Pressure Rating: Match the valve size to the pipeline diameter and ensure it meets or exceeds the system’s pressure rating requirements to prevent leaks or damage during operation.
- Temperature Rating: Choose a valve compatible with the operating temperature range without compromising performance or safety.
- Actuation: Choose manual or automated operation based on control requirements. Options include manual, pneumatic, electric, or hydraulic actuation, each offering different levels of automation and control precision.
In conclusion, butterfly valves are versatile and cost-effective solutions for fluid flow control across various industries. By understanding their components, advantages, disadvantages, and proper usage, businesses can harness the full potential of butterfly valves to optimize their processes and enhance efficiency.