Floating ball valves are essential components in many fluid control systems. This article will delve into what they are, how they work, their components, their advantages, and how to select the right one for your application.
What is a Floating Ball Valve?
A floating ball valve is a quarter-turn valve used primarily in industrial settings to control the flow of liquids or gasses through pipelines. Its design features a floating ball within the valve mechanism, allowing for quick and efficient opening and closing.
How Does a Floating Ball Valve Work?
- Construction: A floating ball valve has a hollow valve body with inlet and outlet ports, a spherical ball, a stem, and a lever to control the position of the ball.
- Ball Design: The ball inside the valve has a central hole (or bore), allowing fluid flow when open. This ball is typically made of metal, such as stainless steel, or other materials chosen for compatibility with the specific fluid being controlled.
- Operation: When closed, fluid pressure pushes the ball against the valve seat, creating a tight seal. To open the valve, the ball rotates 90 degrees (a quarter-turn). This aligns the hole in the ball with the flow path, allowing fluid to flow through.
- Floating Design: Unlike a trunnion-mounted ball valve, where the ball is fixed in place by a top stem and bottom trunnion, a floating ball valve’s ball is connected only to a top stem. This allows it to “float” within the valve seats, held in place by fluid pressure when the valve is closed.
Components of Floating Ball Valves
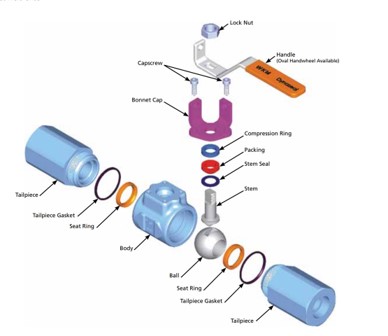
The materials used in a floating ball valve are carefully chosen for strength, corrosion resistance, and compatibility with the specific fluid it will control. Typical components include:
- Valve Body: The valve body is the main housing of the valve and is usually made from materials such as carbon steel, stainless steel, alloy steel, or cast iron. The choice of material depends on factors such as pressure rating, temperature range, and chemical compatibility with the fluid.
- Ball: The ball, the heart of the valve, directly controls fluid flow. It’s typically made from durable, corrosion-resistant metals like stainless steel, brass, or bronze. Coatings or surface treatments may be added to enhance wear resistance and sealing performance further.
- Seats: The valve seats provide the sealing surfaces for the ball when the valve closes. They’re typically made from resilient, wear-resistant materials like PTFE (polytetrafluoroethylene), PEEK (polyetheretherketone), or reinforced elastomers such as Viton or EPDM. These materials ensure a tight seal and resist chemical attack.
- Stem: The stem connects the actuator (lever or other control mechanism) to the ball, transferring the rotational motion needed to open or close the valve. It’s made from corrosion-resistant alloys to ensure reliable operation in harsh environments.
- Seals and Packing: Seals and packing materials are used to prevent leakage around the stem and other moving parts of the valve. These components are often made from elastomers such as Nitrile, Viton, or EPDM, as well as PTFE-based materials, depending on the application requirements.
- Actuator: The actuator controls the valve’s opening and closing. It can be manual (e.g., handle, lever) or automated (e.g., gearbox, pneumatic or electric motor). The actuator type depends on the desired level of control and the specific application.
Industries Using Floating Ball Valves
Floating ball valves are versatile components used in various industries where fluid control is essential. Here’s a breakdown of their common applications:
- Oil and Gas: Pipelines, refineries, and processing plants, handling various hydrocarbons.
- Petrochemical: Controlling the flow of chemicals, solvents, and other fluids in production processes.
- Chemical Processing: Handling corrosive or hazardous liquids where a tight seal is critical.
- Power Generation: Isolating sections of steam, water, or fuel lines in power plants.
- Water and Wastewater Treatment: Controlling flows within treatment facilities, pump stations, and distribution networks.
- Residential and Commercial Buildings: Controlling water flows in plumbing and HVAC systems.
Advantages of Floating Ball Valves
- Affordability: Floating ball valves are a cost-effective solution for many applications, making them a popular choice in cost-sensitive industries.
- Lower Maintenance: Floating ball valves typically have fewer components and simpler designs, making them easier to maintain and repair compared to other types of valves. This can result in lower downtime and maintenance costs.
- High-Quality Tight Seal: Floating ball valves provide a tight seal when closed, minimizing leakage and ensuring efficient flow control. This makes them flexible, versatile, and highly adaptive for applications where sealing performance is essential.
- Low Torque: Floating ball valves require lower operating torque than other valve types, making them easier to operate by hand or with actuators.
Disadvantages of Floating Ball Valves
- Limited Pressure and Temperature Range: Floating ball valves have limitations in high-pressure and high-temperature applications compared to more robust designs like trunnion-mounted ball valves. In extreme conditions, they may be more prone to damage.
- Limited Size Range: Floating ball valves are typically limited to smaller sizes, making them less suitable for large-diameter pipelines or very high-flow applications.
- Cavitation Damage: Floating ball valves may be more susceptible to cavitation damage than other valve types, especially in high-pressure applications. Cavitation occurs when rapid pressure changes cause vapor bubbles to form and then collapse, potentially eroding valve components.
- Potential Seat Wear: The floating ball design can cause wear on valve seats over time, especially in applications involving frequent cycling or abrasive fluids.
How to Choose the Right Floating Ball Valve
To select the right floating ball valve, carefully consider:
- Operating Conditions: Evaluate the specific pressure, temperature, and fluid properties of your system.
- Size and Connections: Choose the correct valve size and ensure the connection type matches your piping.
- Materials: Select materials (body, ball, seats) that are compatible with the fluid and environment to ensure durability and prevent corrosion.
- Pressure and Temperature Ratings: Ensure the valve can handle the maximum pressure and temperature it will encounter.
- Sealing Performance: Look for valves with a proven track record of reliable sealing, especially if leakage is a major concern.
- Actuation: Decide between manual (lever, handle) or automated (pneumatic, electric) operation based on your application needs.
- Reliability and Reputation: Research the manufacturer’s reputation and choose a valve known for quality and longevity.
- Cost vs. Value: Balance initial cost with long-term performance and maintenance requirements to determine the best overall value.
Now that you understand the basics of floating ball valves, you’re equipped to make informed decisions for your fluid control needs. Remember to prioritize operating conditions, materials, size, and reliability when making your selection.