Plug valves stand out as versatile components crucial for controlling the flow of various substances within pipelines. Their simple design and reliable operation make them a popular choice for controlling liquids, gasses, and slurries. This comprehensive guide delves into the world of plug valves, exploring their workings, components, materials, and various types. It also sheds light on their advantages, disadvantages, and crucial factors to consider when selecting the right plug valve for your needs.
What is a Plug Valve?
A plug valve is a type of quarter-turn valve that uses a cylindrical or tapered plug to control the flow of fluids within a pipeline. This valve is recognized for its simple yet effective design, making it a popular choice in various industries for flow regulation, on/off control, and throttling applications. Plug valves are versatile and can handle a wide range of fluids, including corrosive chemicals, oil, natural gas, water, wastewater, acids, sewage, and steam, by selecting appropriate materials for the plug and body.
How Does a Plug Valve Work?
The operation of a plug valve is straightforward. The cylindrical or tapered plug within the valve body can be rotated to open, close, or throttle the flow of fluid. When the plug is turned, the hole within it aligns with the pipe to allow fluid to pass through or block the flow when perpendicular to the pipe. This simple yet effective mechanism allows for quick and reliable control of fluid flow within a pipeline.
Components of a Plug Valve
A plug valve consists of several key components that work together to control fluid flow effectively:
- Body: The main structure that houses the plug and provides connection points for piping.
- Plug: The rotating element that controls flow.
- Stem: Connects the plug to the actuator and facilitates plug rotation.
- Actuator: Mechanism for manually or automatically operating the plug.
- Seats: The surfaces against which the plug seals when closed, preventing leakage.
- Seals and Bearings: Ensure tight sealing and smooth operation of the plug within the valve body.
Materials of Plug Valves
Plug valves are constructed from various materials to suit different applications and fluid types. Common materials used for plug valves include carbon steel, stainless steel, cast iron, bronze, and advanced alloys. The choice of material depends on factors such as the type of fluid, pressure, temperature, and corrosion resistance required for the specific application.
Types of Plug Valves
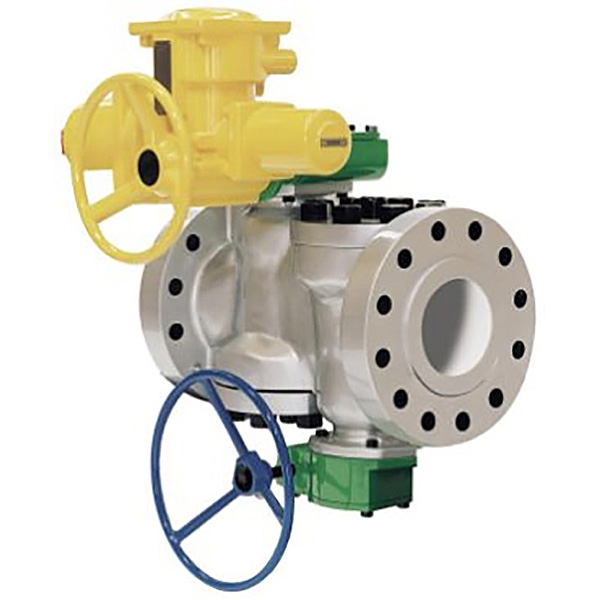
Plug valves come in different types, each with unique features and advantages:
- Lubricated Plug Valve: Uses a lubricant to reduce friction and seal ports, suitable for applications with mildly abrasive particles.
- Non-Lubricated Plug Valve: Utilizes a polymeric sleeve to reduce friction, ideal for applications where maintenance needs to be minimal.
- Eccentric Plug Valve: Features a half plug design for higher seating force and improved shut-off capabilities.
- Expanding Plug Valve: Mechanically expands to provide double block and bleed function, preventing product contamination.
Plug Valves Uses
Plug valves find application in a wide range of industries due to their versatility and reliable performance. Here are some common uses:
- Oil and Gas Industry: For on/off control of pipelines transporting oil, gas, and refined products.
- Chemical Processing: Handling various corrosive and abrasive fluids in chemical plants.
- Water and Wastewater Treatment: Regulating flow in water treatment facilities and wastewater treatment plants.
- Power Generation: Controlling the flow of fluids in power plants, including water for cooling and steam for turbines.
- Mining Industry: Regulating the flow of slurries and abrasive materials in mining operations.
- Food and Beverage Industry: Handling sanitary fluids in food and beverage production processes.
- Marine Applications: Used on ships and offshore platforms for controlling flow of various fluids.
The extensive use of plug valves across these industries highlights their adaptability and effectiveness in diverse flow control applications.
Advantages of Plug Valves
Plug valves offer several advantages that make them a popular choice for various applications:
- Simple and Reliable Design: The straightforward quarter-turn operation and robust construction minimize the risk of malfunctions and ensure reliable performance.
- Leak-Proof Closure: The precise sealing surface between the plug and seat provides a tight shut-off, minimizing leakage even with harsh fluids.
- Low Maintenance: Plug valves generally require minimal maintenance compared to more complex valve designs.
- Versatility: They can handle a wide range of fluids, including liquids, gasses, and slurries, making them suitable for various applications.
- Bi-Directional Flow: Certain plug valve designs allow flow in both directions, offering operational flexibility.
- Pressure Drop: Full-bore plug valves minimize pressure drop across the valve when open, reducing energy consumption in pipelines.
- Cost-Effective: They are generally more affordable compared to some other valve types, making them an attractive option for many applications.
Disadvantages of Plug Valves
While offering numerous advantages, plug valves also have some limitations to consider:
- Limited Throttling Capability: Primarily designed for on/off applications, throttling flow for extended periods can cause wear on sealing surfaces.
- Torque Requirement: Larger-sized valves, especially non-lubricated ones, may require higher torque for operation, necessitating larger actuators.
- Shear Stress: The plug can experience shear stress when partially open, potentially leading to accelerated wear.
- Stagnant Flow Areas: Some plug valve designs may have small pockets where fluid can stagnate, potentially leading to issues like settling of solids or bacterial growth.
- Not Ideal for Frequent Cycling: Frequent opening and closing can cause wear and tear on the sealing surfaces, reducing valve lifespan.
How to Choose the Right Plug Valves
Selecting the right plug valve for your application requires careful consideration of several factors:
- Fluid Type: The type of fluid being handled (liquid, gas, slurry) and its properties (corrosiveness, abrasiveness) will influence material selection for the plug, seat, and body.
- Pressure and Temperature Rating: The valve’s pressure and temperature ratings must exceed the maximum operating conditions of the pipeline.
- Flow Rate and Direction: Consider the required flow rate and whether bi-directional flow is necessary. Full-bore valves may be preferred for high flow rates.
- Operation: Evaluate the frequency of operation (on/off or throttling) and choose a valve design suitable for the intended use.
- Maintenance Requirements: Consider the ease of maintenance and access to the valve for potential repairs.
- Cost: Balance the initial cost of the valve with its performance, maintenance requirements, and expected lifespan.
Consulting with valve manufacturers and considering these factors will ensure you select the most appropriate plug valve for your specific needs.
In conclusion, plug valves are essential components in fluid control systems, offering a reliable and efficient solution for regulating flow in various industries. Understanding the working principles, components, types, uses, advantages, disadvantages, and selection criteria of plug valves is crucial for choosing the right valve for specific applications.