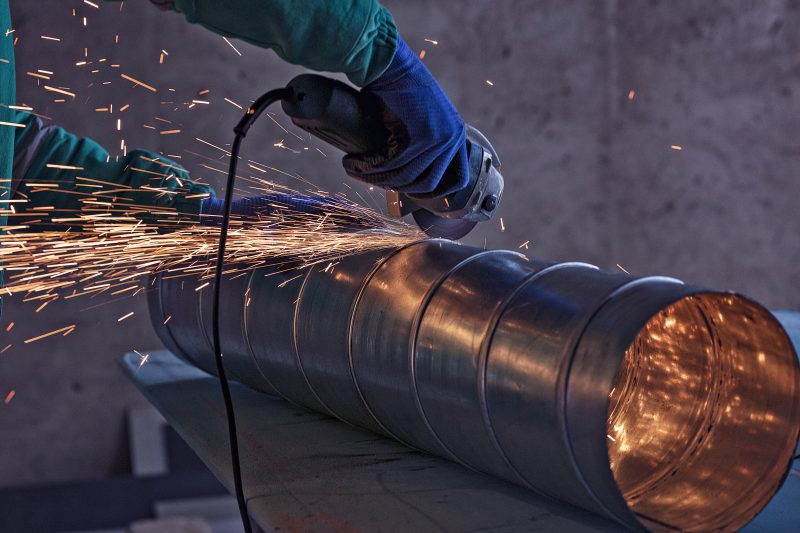
Steel pipes are cylindrical steel tubes that are utilized in a number of industrial and infrastructural applications. They are the most often utilized product in the steel industry. Pipe is mostly used to transport liquids or gases underground, such as oil, gas, and water. Despite this, pipes of varied diameters are widely used in industry and construction. A common example of home manufacturing is the thin steel tubing that powers the cooling mechanism in refrigerators. In the building industry, pipes are utilized for heating and plumbing. Handrails, bike racks, and pipe bollards may all be made out of steel pipe of different sizes.
Steel Pipe Manufacturing Process
This ubiquitous building material is created in two unique techniques, beginning with the melting of raw components and ending with the molding or welding of completed products:
1. The first stage is to transform raw steel into a more useable form.
Both methods must start with the manufacture of high-quality steel. Raw steel is produced at foundries by melting raw materials in a furnace. Components may be added to the molten metal and impurities removed to exactly balance the composition. After that, the molten steel is either poured into molds to make ingots or transferred to a continuous casting process to produce slabs, billets, and blooms. Pipe is made from slabs or billets of steel.
2. Steel slabs and steel skelp in pipe manufacturing
Slabs are heated to 2,200 degrees Fahrenheit to make steel skelp. The heat causes a scale to build on the surface, which must be cleaned using a scale breaker and high-pressure cleaning. After the steel slab has been cleaned, it is hot rolled into thin, narrow steel strips known as skelp. Skelp is pickled (surface cleaned) using sulfuric acid before being washed and rolled into massive spools as a raw material for pipe manufacturing. The width of the skelp determines the diameter of the pipe that may be manufactured.
Steps to completion
Pipes may be straightened as a last manufacturing process before being joined. Threaded couplings are often used in small bore pipe, while welded-on flanges are used in larger bore piping. For quality control purposes, measuring equipment verifies the finished pipe’s measurements and stamps the information on the pipe’s side.
Control of quality
Using x-ray equipment to check the pipe for faults, especially along the weld, is one of the quality controls processes. Another way is to pressure test the pipe by filling it with water and then holding it under pressure for a certain amount of time to identify any defects that might lead to catastrophic collapse before putting it into service.
Steel pipe Utilization
Pipes are used in many different purposes, including as building, transportation, and industrial. They are measured by their exterior diameter, with the interior diameter varying according to wall thickness. Certain applications need thicker walls than others, depending on the stresses that the pipe must handle.
Utilization in structures
In architecture and construction, structural applications are common. Steel tubes are a phrase that is often used to refer to the building material in a variety of industries.
Pipes used in construction
Steel tubes are used to strengthen foundations using a procedure known as piling. In these cases, the tube is driven deep into the earth before the foundation is laid. It provides stability for a towering building, or a structure built on unsteady ground. Fundamentally, pile foundations are of two types:
- End bearing piles have a bottom end that is supported by a thick layer of soil or rock. The load of the building is communicated to the strong layer through the pile.
- Friction piles transfer the weight of the building to the soil by friction across the whole height of the pile. The pile’s whole surface area contributes to force transmission to the earth.
Poles for scaffolding
Scaffolding poles are constructed by connecting steel tubes in a cage to provide access to places above ground level for construction workers.
Industrial application
Guard rails: constructed of steel tubing, they are used to protect cyclists and pedestrians. Guard rails, which are also made of steel tubes, are an appealing safety feature for stairs and balconies.
Bollards: Bollards are used to safeguard people, buildings, and infrastructure by separating them from motor traffic.
Bike racks: Steel tubes are bent to form a huge range of commercial bike racks. Steel’s strong material properties make it impregnable to intruders.
Transportation use
Steel pipes are the most often utilized material for product transportation since they are well-suited for long-term installations. It can be buried underground because to its hardness and resistance to disintegration. Low pressure applications do not need the use of robust pipes since they are not exposed to significant stresses. A small wall thickness allows for a more cost-effective production procedure. Specifications for more specific applications, such as pipes used in the oil and gas industry, are more stringent. Because of the hazardous nature of the chemical being transported and the possibility of increased pressure on the line, a high degree of strength and hence a thicker wall are required. This frequently results in a higher price. Quality control is critical for these applications.
Steel pipes, which are used to transport items such as oil, gas, and water, are perfect for long-term installations.
Procedure for specifying steel pipe
There may be some confusion about how these materials are defined and what they mean in terms of the actual qualities of the pipe. The three most often referenced organizations in North America for pipe standards are the American Society for Testing and Materials (ASTM), the American Society of Mechanical Engineers (ASME), and the American Petroleum Institute (API). Specifications are divided into three categories:
1. Pipe nominal diameter
“Nominal Pipe Size,” or NPS, is the acronym for pipe size. The origins of NPS values for smaller diameter pipes (NPS 12) differ from those for bigger diameter pipes. However, all pipes with the same NPS number have the same outside or outside diameter (OD). Internal diameters vary depending on the thickness of the metal’s wall. This is done to guarantee that the same structural supports may be used for all pipes with the same NPS value, regardless of wall thickness.
2. Schedules
Steel pipe schedules are a means of specifying the wall thickness of a pipe. This is an important feature since it has a direct link with the pipe’s strength and suitability for certain applications. Given the design pressure and allowable stress, a pipe schedule is a dimensionless number that is calculated using the wall thickness design formula. Here are some examples of schedule numbers: The most common schedules are 5, 5S, 10, 20, 30, 40, 50, 60, 80, 100, 120, 140, 160, STD, XS, and XXS. The schedule number denotes the thickness of the pipe’s wall. The inner diameter of a pipe is defined by the schedule number, just as the OD is determined by the NPS number.
3. The pipe’s weight
The NPS (outside diameter) and the schedule may be used to calculate the weight of a pipe (wall thickness). The constant is calculated using steel’s theoretical weight of 40.8 pounds per square foot per inch of thickness: W = t (OD – t) multiplied by 10.69
Where:
- W represents for weight (in pounds per foot).
- OD stands for outer diameter; and
- t stands for thickness.
4. Certification
A Material Test Report, also known as a Mill Test Report, is provided by manufacturers to confirm that the product meets the stipulated chemical analysis and mechanical qualities. The MTR will contain all relevant product information and will accompany it throughout its life.
Some of the common parameters that an MTR may record are as follows:
- The material’s chemical makeup, including the quantity of carbon, alloys, and sulfur.
- Material dimensions, weight, identity, and grade
- The heat number of the material, which corresponds to the processing batch; and
- Tensile strength, yield strength, and elongation are mechanical qualities. The most often referenced steel bollard standards are ASTM A53 and ASTM A500.
For Oil & Gas and Petroleum Business, the types or the standard for the steel or metal pipes that has been used widely is API (American Petroleum Institute) standard. We call the pipes manufactured according to API standard as “API Pipes”
API Pipe
API Line Pipe is a kind of steel pipe used to carry crude oil, natural gas, and petroleum distillates. Line pipes, as opposed to casing and tubing, are used to create pipelines. Line pipes are manufactured in compliance with the specifications of the American Petroleum Institute (API). API 5L is a standard developed by the API that specifies the dimensions, physical, mechanical, and chemical properties of steel. API 5L pipes are manufactured at a number of pipe mills across the globe for the oil and gas industry.
API 5L Pipes
API 5L Pipes are a kind of pipe. Let’s look at how they’re manufactured, their composition, their uses, and some of the potential benefits they provide.
The American Petroleum Institute is abbreviated as API. The API 5L standard, in general, defines specifications for pipe used in the natural gas and oil industries for the transportation of gas, water, and oil. API 5L is a seamless and welded steel line pipe standard. It includes plain-end, threaded-end, and belled-end pipe, as well as TFL pipe and pipe with particular coupling ends.
Desulphurization and API 5L pipe strength
Manganese sulfides are an important component of manganese alloyed steels. Sulphure content should be maintained to a minimal due to their inclination for segregation, which results in diminished impact strength. We set a limit of 0.007 percent.
Benefits and applications of API 5L pipe
- Transportation of gas, water, and oil – ideal for long pipes due to cheap cost
- Pipeline steel – fracture propagation resistance
API Line Pipe Specifications and Standards
API 5L specification includes seamless and welded steel line pipe used in the petroleum and natural gas industries for pipeline transportation systems. The API 5L standard is intended for the transportation of gas, water, and oil.
API 5L requirements adhere to the ISO 3183 standard, which standardizes pipeline transportation systems in the materials, equipment, and offshore constructions used in the natural gas, petroleum, and petrochemical industries. The technical committee recognized the presence of two essential Product Specification Levels (PSL) of technical requirements while creating the standards and so produced PSL 1 and PSL 2. PSL 1 is the bare minimum for line pipe quality, while PSL 2 contains additional chemical, mechanical, and testing standards.
This standard applies to the grades A25, A, and B, as well as the “X” grades X42, X46, X52, X56, X60, X65, X70, and X80. The two-digit number after the “X” signifies the Minimum Yield Strength (in thousands of pounds per square inch) of pipe made to this grade.
We encounter several casing and pipe piling needs that necessitate the use of API 5L steel pipe. This pipe was created to be used in natural gas and petroleum transportation pipelines. Although API 5L is an excellent product, it is typically not meant for structural reasons when used in casing and pipe piling projects.
Quality Control Procedures used for API 5L Pipe
The American Petroleum Institute’s API 5L Specification for Line Pipe defines criteria for seamless and welded steel pipe used in petroleum and natural gas transportation networks. Comprehensive testing, including hydrostatic testing, nondestructive testing, and destructive testing, is required to achieve this aim.
1. Testing for Hydrostatic Pressure
A hydrostatic test is a safe means of checking the strength and leaking of pressure retention equipment. The required pressure varies according on the diameter, thickness of the wall, and material grade.
2. NDE
All welded seams, including longitudinal and circumferential seams, need radiographic and ultrasonic testing, abbreviated RT and UT. These tests ensure that all welds are free of flaws.
3. Destructive Testing
Destructive testing is a group of analytical procedures used to assess the properties of materials, components, or welds by evaluating a sample of the product to determine its failure point. It requires extracting a sample of the product and submitting it to a laboratory for testing. Destructive testing is used to determine the load bearing capability of a material.
Substitutes for API 5L Pipe
Consider the following API 5L alternatives:
A252 (ASTM)
ASTM A252 American Society for Testing and Materials (ASTM) “A252, Standard Specification for Welded and Seamless Steel Pipe Piles” may be adequate for the majority of casing constructions. T BAILEY Inc. will use this standard if no alternative specifications are specified in the request for quote. This pipe standard is often utilized in Department of Transportation projects. Because it demands 100% visual inspection and dimension verification, A252 is the most cost-effective alternative to API 5L.
API 2B (non-monogramed)
The “API 2B Specification for the Fabrication of Structural Steel Pipe” is identical to ASTM A252. API 2B, on the other hand, undertakes extra quality control on welded seams, such as 100% visual inspection, 100% RT or UT of circumferential seams, and 10% RT or UT of longitudinal seams. In addition, additional criteria may be incorporated to ensure compliance with other specified requirements.