General Twin Seal Plug Valve
Cameron GENERAL Twin Seal double blockand-bleed plug valves established the standard specifications for high-integrity, positive shutoff valves. For both inline testing and simple field maintenance and repair, aviation fuel, facility managers, engineers, and contractors rely on GENERAL Twin Seal valves for fuel delivery with positive, provable segregation.
Rapid seal abrasion is inherent in the designs of most ball and gate valves. The double block-and-bleed (DBB) Cameron GENERAL VALVE Twin Seal plug valve reduces this constant wear by using two seating slips mounted independently on a tapered plug by dovetails, which mechanically retract from the seating surface prior to rotating. This provides a bubble-tight verifiable dual seal without seal abrasion.
Standard
- Twin Seal Design
- Designed to ASME B16.34 and API 6D
- Fire Tested to API 6FA or API 607
- Meets API 6D DBB and DIB1
- Mechanical Sealing
How It Work
Zero-Leakage Double Block-and-Bleed Plug Valve with Retracting Seals
The GENERAL Twin Seal valve helped establish the rigid requirements of double block-and-bleed service. The valve is a nonlubricated, resilient seal, expanding plug-type valve that has a mechanical means of freeing the plug before it is rotated from the closed to open position. The plug and seal slips rotate freely with no seal-to-body contact, eliminating seal abrasion and wear.
a double block-and-bleed service or DBB valve is a “single valve with two seating surfaces that, in the closed position, provides a seal against pressure from both ends of the valve, with a means of venting/bleeding the cavity between the seating surfaces.
Why do General Twin Seals’ require a bleed?
- Per API 6D a pressure relief device must be provided on all double block and bleed valves in liquid service.
- Relieve excess body pressure due to thermal expansion
- Verify seal integrity
- When valves filled with 330 API fuel oil have exhibited a 75 psi increase in pressure with a temperature rise of only 1°F. Putting this into perspective, a normal daily 30°F swing in ambient temperature may cause an increase of body cavity pressure of 2250 psi.
Actucation
- Multi-turn electric actuators
- Hydraulic Operators
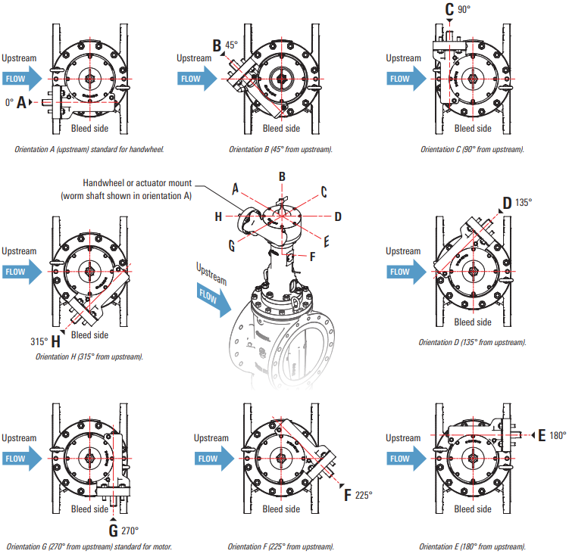
Installation Orientation
Applications
- Pipeline pumping stations and terminals
- Refinery bulk loading terminals
- Aviation and naval fueling systems
- Crude oil and refined products metering and measurement systems
- Pig launcher and receiver systems
- Other specialty applications in industrial process plants

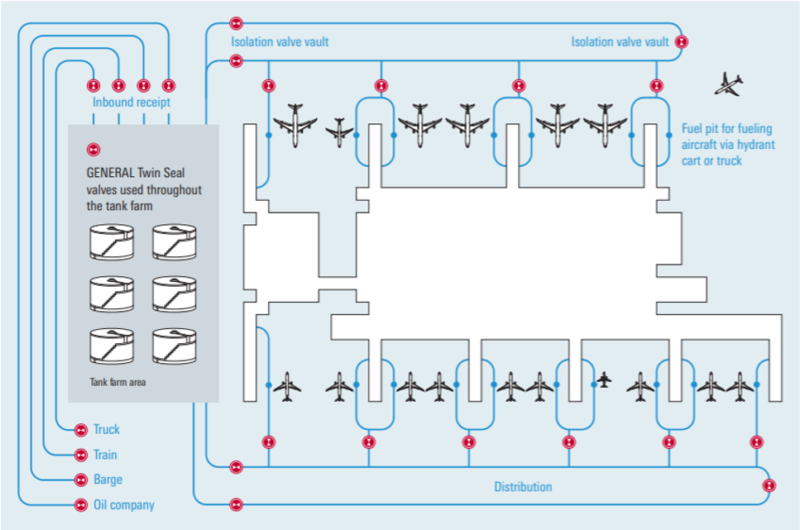
Product Detail
Series |
Size, in [mm] | ASME |
Percent Open, % |
900 |
2–24 [50–600] | 150–600 | 100 |
200 |
2–6 [50–150] |
150 | 70 |
2–4 [50–100] |
300 and 600 | 70 | |
8800A |
8–36 [200–900] |
150 |
70 |
6–30 [150–750] | 300 and 600 |
70 |
|
800 | 2–42 [50–1,050] | 150–1500 |
70 |
400 | 6–24 [150–600] | 150–600 |
40 |
General Twin Seal Plug Valve Configuration
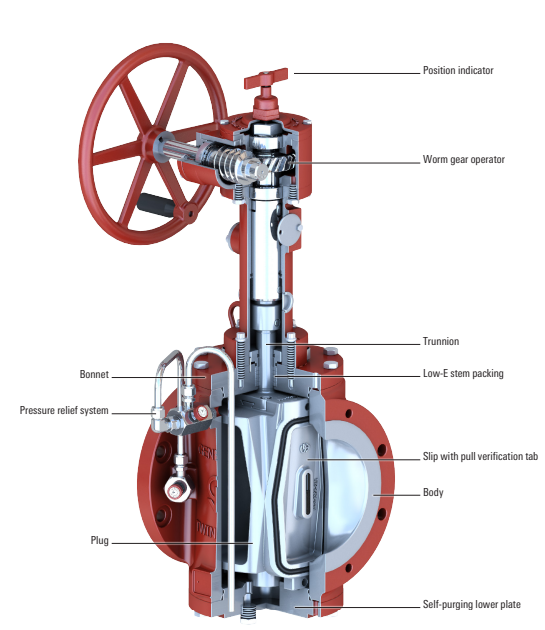
Model 8800A Features and Benefits
- Low-E certified design
The GENERAL VALVE Twin Seal plug valve model 8800A provides a fully fugitive emissions–qualified design as standard, with Low-E packing that is tested and qualified to API 622 and 624 standards. The design is certified to ISO 15848-1 with the highest endurance class of CO3.
- Modular plug
The patented modular plug design offers a redundant mechanical connection between the upper trunnion and plug to enable flexibility for upper trunnion material to meet customer needs. This unique design provides the ability to service and replace the trunnion in the field without replacing the entire plug.
Manganese phosphate–coated slips eliminate surface corrosion and are available with more than 17 elastomers to meet most fluid needs. A pull-tab design is used to demonstrate the bond between the elastomeric seal and the slip; Cameron’s proprietary in-house bonding ensures superior quality control. Slip exchange and a rebond program are available
The self-purging lower plate is specially designed to automatically flush the lower trunnion with each valve cycle, which prevents accumulation of particles and dirt in the lower part of the valve body. This design ensures consistent and reliable valve operation.