What does the term “asset integrity” means in oil and gas industry?
Asset integrity, also known as asset integrity management systems (AIMS), is the term used to describe an asset’s ability to operate efficiently and accurately while also protecting the health and safety of all personnel and equipment with which it interacts – as well as the measures in place to ensure the asset’s long-term availability. Throughout the life cycle of an asset, from its conception through decommissioning and replacement, asset integrity must be maintained.
Asset integrity management consists of a number of components
Much of the oil and gas industry’s infrastructure is already nearing or has already reached the end of its operational life expectancy, if not already beyond it. Because the cost of replacing assets, as well as the resulting turnaround time, has become unacceptably expensive for so many facilities, asset integrity has now surpassed concepts such as OPEX and Agile as the watchword on everyone’s lips, according to a recent study.
There is an increase in challenges such as vessel inspection, which is a significant contributor to production downtime; and corrosion under insulation, which is a frequent cause of sudden shutdowns; and taking the step to employ new solutions is becoming a necessity in many locations, particularly offshore.
The importance of the human factor
Asset integrity is based on the assumption that the vast majority of people within the organization will carry out their responsibilities correctly. However optimistic this may sound, the vast majority of maintenance, inspection, and data management activities are carried out with the best of intentions. Things, on the other hand, are not always accomplished completely or in the shortest amount of time available. It is unlikely that simple measures, such as increased inspection frequency, can uncover every overlooked problem. It is also unlikely that employees, who are required to increase their inspection labor or who are involved in missed problems, will be enthused about the task at hand.
Some indicators that everything is not well in the field of asset integrity management and inspection include the following:
- Teams believe that any concerns they have regarding health and safety, or the condition of equipment are not taken seriously, resulting in an atmosphere where errors are not even reported as a result of this perception.
- Any modifications to asset integrity plans, or even the fundamental operation of the facility, are only implemented after a large-scale event.
- An inability to distinguish underlying causes from basic defect reports, which often leads to personnel being lulled into an unwarranted feeling of security and overstating the extent to which the facility is safe and operating.
- Tactic knowledge, rather than a physical and immediately available set of rules, is relied upon in the context of AIM and reporting problems.
- In the world of maintenance contractors, there is a “lowest bidder” mentality that prevails, and knowledge of and passion for asset integrity are not highly rewarded.
The very real outcome of this kind of environment is that nothing occurs in any meaningful way. Till a significant occurrence forces an organization to adjust, which is typically at tremendous expense, asset integrity is seen as a barely acceptable inconvenience, a type of obstacle to getting the job done properly.
Identifying and filling up the gaps in asset integrity management systems
Despite the fact that there are more AIM systems on the market now than at any previous time in history, there are still no one-size-fits-all solutions available. Although no inspection plan or database can possibly address all of the AIM concerns that might occur, integrity systems are nevertheless seen as distinct from the rest of the organization’s activities. Employees may be reluctant to accept responsibility for their actions, seeing the suite of AIM packages as an effort by the corporation to police them rather than as an intrinsic part of their job description.
The holes in AIM packets must be filled with the vigilance of the same persons from whom they are intended to protect, but a creative strategy may be required to guarantee that this message is received by the intended recipients.
What is the significance of asset integrity management?
A leak from the Piper Alpha oil platform in the North Sea occurred over the period of 22 minutes on July 6, 1988, causing an explosion that killed 167 of the rig’s 229 employees. The leak occurred over the length of 22 minutes. Among other things, this accident is seen as a watershed point in the development of current approaches to both EH&S and AIM in the oil and gas industry, not least because it resulted in each offshore operator investing £1 billion in safety measures.
The United Kingdom government subsequently launched a public enquiry, which was completed in 1990 and made 106 recommendations on how to implement HS&E and AIM initiatives more effectively in the future – all of which were approved by the oil and gas sector. So, given that we are living and working in an era when significant AIM attempts are being made, what areas should individuals be concentrating their energies on?
Developing a strategic approach to AIM
According to research performed by Oil & Gas IQ, oil and gas operators are increasingly pursuing price-responsive strategies as well as the optimization of existing assets in order to remain competitive. These enterprises, particularly those operating in the North Sea, are now re-evaluating their business processes in order to stay afloat. 51 percent of oil and gas experts are now working on installations that are more than 20 years old and have been in service for more than a decade — with fewer than a third working on installations that are in their first ten years of operation.
More than half of asset integrity professionals have had their budgets reduced, and the average grade given to those professionals’ own firms’ asset integrity management (AIM) rating was 5.4 out of a possible 10. Only 52% of respondents believed that their job load was manageable in terms of achieving objectives and preserving safety – despite the fact that the vast majority worked with a meager budget of less than £250,000. Unsurprisingly, asset integrity professionals report that the two most pressing concerns they face are keeping assets under budget and the age of the assets themselves. The lack of communication between departments in oil and gas businesses is by far the most serious fault that has been identified, followed by a lack of a safety culture in the industry. There is definitely work to be done.
RBI: Risk-Based Inspection
It is now more necessary than ever to ensure that an effective system of identification is in place, especially since the industry’s infrastructure is rapidly aging and becoming one of its key issues. For example, more than half of pipelines in the United States are at least 50 years old, with 3,300 incidents, including the worst spill in US pipeline history, eighty fatalities and almost 400 injuries in only the last five years. Despite the fact that it may seem apparent, maintaining integrity, preventing corrosion, and repairing damage is similar to seeing an iceberg from a distance.
It is nearly impossible to implement damage mitigation techniques without the assistance of dedicated and experienced professionals. For every readily apparent symptom of corrosion or asset instability, there are dozens of hidden issues: hydrogen attack, high-temperature tempering, thermal fatigue, metallurgy issues, internal system corrosion, and so on. Once it has been determined that a comprehensive examination is required, the following step is to put it into effect.
Among the methods available are risk-based inspections (RBIs), which demand that the risk be reduced while putting in the least amount of work possible in order to expedite the process and free up more time. The problem is that there are an almost limitless number of methods in which we may carry out our maintenance – and with so many hazards (such as calibration uncertainty or equipment accessibility), quantification is just not viable. In order to determine where on the quantitative/qualitative spectrum a corporation is located, it must first choose whether it will depend more heavily on specialists or on data.
Companies will operate in either a reactive or a proactive mode, depending on how effectively or poorly they foster their dependability cultures. It goes without saying that you want to be proactive. Because of a failure to foresee and monitor for hidden difficulties, you will only be able to respond after problems have developed, which will cost you significantly more money in the long run and reward those who have shown the ability to react swiftly. Instead of enhancing the culture, this positive reward serves to promote the tendency to react rather than act.
Determine the existence of damaging conditions and the variables that influence them
Increasing the temperature of the environment in which an asset is placed will, as no one can be surprised, cause the rate of deterioration to grow dramatically. However, failure to recognize a surge in trace chemicals such as chlorides or hydroxides – or any high- or low-pH substance – will result in the asset being located in a halogen-rich environment.
Even a modest but continuous stream of air into a fuel stream can cause significant damage to pipes, considerably more so than either carbon dioxide or hydrogen-sulphide combined.
The following are some more potentially disastrous combinations that everyone who is serious about protecting asset integrity should be aware of — anything from lead contamination in water to nickel corrosion under acidic circumstances. Although many harmful combinations do not exist in nature, it is possible to ameliorate the majority of them by performing procedures in a clean and exact manner. Believe it or not, steel rigs submerged in saltwater do not endure indefinitely, which has resulted in an increase in the number of specialized coating suppliers in recent decades.
The third aspect that we must take into consideration in order to completely appreciate damage process to the greatest extent possible is fundamental strain. When you add in the tension that comes with the procedure, you get what is known as basic strain (as if it were operating in an ideal world).
Asset Performance Management
Undoubtedly, one of the most difficult tasks in the field of energy infrastructure is the development of a comprehensive asset maintenance and integrity program for a new natural gas processing and liquefaction complex. In order to maintain the company’s social and regulatory license to operate, facility owners must ensure that their equipment displays the proper levels of safety, integrity, and dependability, among other characteristics. Maintaining equipment documentation (as well as recording damage mechanisms for important functions) helps to support these goals and manage operational risk. This allows for improved asset management and helps to reduce operational risk.
The constant business challenge for asset integrity managers is how to balance the designing, maintenance, and replacement of assets throughout their life cycle with the costs to business – in terms of finance, time, and resources. At its heart, it is the managing of the degradation of assets.
In order to effectively manage risk across the asset life cycle, the organization must design a comprehensive asset performance management (APM) plan. The efficient APM solutions, which comprise asset reliability and integrity management, may assist the manufacturing plant in the following ways:
- Increasing the return on investment by using cost-effective and efficient methods
- Keeping an organization’s license to operate by implementing sustainable HSE procedures is important.
- Increasing the safety and dependability of operations by addressing whole life cycle risk
- Using asset performance management (APM) solutions such as asset integrity management and enterprise asset management, you may continuously improve productivity and profitability (EAM)
Business Requirements
- Developing a risk-based, enterprise-level strategy for controlling business processes and asset performance criteria can help you achieve your goals.
- Establish a proactive integrity program in order to decrease inspection expenses.
- Ensure that the most effective and efficient EAM system and procedures are in place for the management of assets, inventories, documentation, and workflows.
- Provide on-going assistance with program creation and training services.
Solutions
In order to establish a complete APM strategy, it is necessary to use the Reliability Based Maintenance approach, which has been validated and is technically adequate for improving asset management programs and operational efficiency. The solutions will be centered on people, work processes, systems, technologies, governance, infrastructure, policies, and scope of work, among other factors. They show how LNG operators may design bespoke solutions for safety and risk management, operational excellence and organizational sustainability.
Asset Integrity Management should be established
APM plans for energy infrastructure should include the development and implementation of asset integrity management programs, which should include the following activities: project management, strategy development and business processes, asset register and management information system (MI), preventive maintenance program development, spare parts and bill of materials development, and data asset management services. In order to preserve the integrity of facilities and business processes throughout the firm, plant managers will benefit from these efforts in monitoring asset safety, dependability, and efficiency.
Reduce the cost of inspections
Development of an inspection work process connected to damage mechanism assessment, risk-based inspection (RBI), equipment/piping systemization, and condition monitoring location (CML) positioning are also included in the management plan. A considerable cost reduction for the customer was realized as a consequence of the more technically based and robust assessment of inspection and nondestructive evaluation (NDE) requirements as a result of these work methods.
For example, the work procedures for pipe systemization and CML installation have resulted in the following reductions:
- There will be an approximately 20% decrease in the number of piping circuits (based on another consultant’s circuitization of the piping), which will result in an approximately 20% reduction in the cost of piping inspection.
- There has been a 50 percent to 60 percent decrease in the number of pressure vessel and piping CMLs (when compared to the standard CML placement technique); this reduction has been achieved by our CML placement approach, which is based on damage mechanisms and risk.
- Without taking into account the effect of our RBI analytical technique, the two inspection cost reductions correspond to an estimated 30 percent decrease in inspection and NDE needs for the new process, with an anticipated savings of USD 300,000 each inspection cycle.
Delivered Benefits
Asset health monitoring and maintenance solutions that use a comprehensive, risk-based approach are helping a large LNG export plant increase efficiency in the planning, inspection, and repair processes, resulting in safer, more dependable, and longer-lasting operations. It might also assist facility managers in improving their awareness of possible risks that could cause company operations to be disrupted if vital systems are compromised via the use of data-driven risk and reliability solutions and integrated EAM system services, among other things. Equipment reliability data may be analyzed and prioritized using a statistical technique. This approach allows for more efficient asset performance, which is important for attaining safety and productivity advantages.
In order to avoid unscheduled shutdowns of LNG liquefaction plants, maintenance and reliability are essential
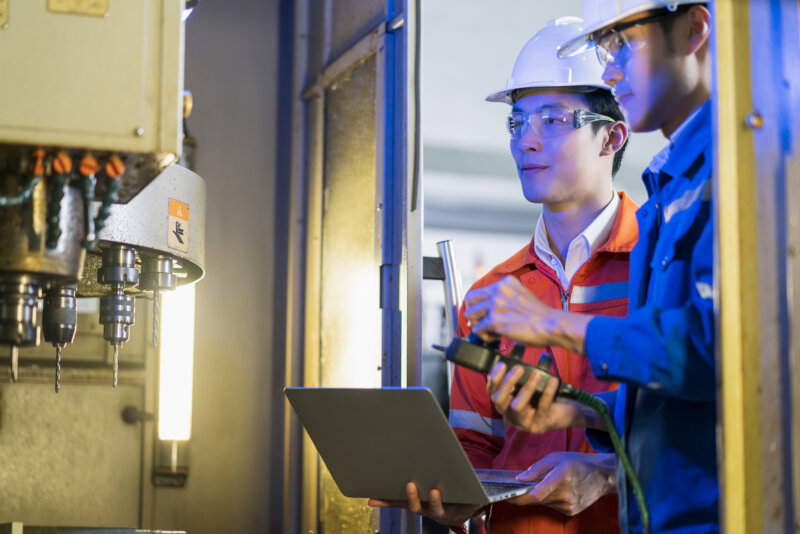
Despite the fact that an unforeseen shutdown is an integral aspect of an operating plant’s operational and safety management system, unplanned shutdowns for a contemporary LNG liquefaction operating facility are often among the most expensive occurrences for the facility’s owner. As a result of the loss of output and reputation, each of these occurrences has a detrimental impact on the owner’s firm. Considering how quickly the world is moving toward renewable energy sources, the advantages to LNG owners of implementing an advanced preventative and maintenance program to avoid unscheduled shutdowns are both evident and financially reasonable.
There are difficulties in avoiding unexpected shutdowns. An unexpected or emergency shutdown of an operational facility due to safety, asset, or environmental hazards is an essential step for facility owners to restore the process and equipment to a safe condition in an emergency. In the case of a contemporary LNG liquefaction plant, unscheduled shutdowns are sometimes frustrating occurrences for the facility’s owners because of the loss of output, which may amount to millions of dollars per day.
LNG plant operators have a number of issues, including preventing unexpected shutdowns and developing effective solutions in the following areas:
- A contemporary LNG plant is complicated and large in size, and the possible failures of all components cannot be addressed at the same time during a planned turnaround owing to variances in the component failure rate. In the intervals between planned shutdowns, a failure will always occur at an apparently inconvenient moment owing to randomness or unpredictability, resulting in a seemingly unexpected result.
- In order to ensure steady operation, tens of thousands of active components in an LNG plant must be maintained concurrently and correctly. It is very difficult for a facility’s maintenance personnel to keep up with the demands of the job, particularly when using a preventative maintenance strategy.
- In the early stages of engineering design, identifying the potential risk of all component failures is not a simple job to do. As part of the design, a limited number of unexpected shutdowns are triggered automatically (e.g., through shutdown interlocks). The vast majority of them are triggered manually by the operator based on the condition on site, which places a significant amount of strain on the facility’s operations and maintenance personnel to perform their duties.
Traditional reactive maintenance approaches are less effective in avoiding unexpected shutdowns since the failure and shutdown have already happened when the strategy is implemented.
To ensure the effectiveness of a preventative maintenance program, it is critical to have access to reliable equipment dependability and failure rate information. Sometimes equipment fails sooner than what the manufacturers projected or suggested based on previous data, which makes it more difficult to correct the real turnaround intervals of the equipment when applying a preventative maintenance technique to repair it.
The root reasons of failures that result in unscheduled shutdowns are diverse
Many unexpected shutdowns were caused by design flaws and human mistake, which are typically nightmares for plant managers since they are less tied to equipment aging or wear and tear than they should be. To deal with such failures, a plant maintenance team must use methods that are different from those used in regular plant maintenance.
Unplanned shutdowns may be avoided by using certain strategies. Unplanned shutdowns of large-scale and complex LNG plants need more than merely decreasing or minimizing failure rates. Owners that implement sophisticated preventive and maintenance plans will be the ultimate winners in the long run. While all preventive and maintenance programs have the same overall purpose of preventing equipment failures and reducing downtime, an advanced prevention and maintenance program for an LNG plant should be distinguished by the following characteristics:
- Covering the whole facility’s lifecycle—that is, from engineering design through plant operations—is a must.
Preventive and predictive measures are being used
Advanced technologies, such as computerized maintenance management systems, are being used in the areas of monitoring, data collecting, and data analysis and management, for example.
For an owner to successfully implement such a program, systematic deliberation is required in the selection of engineering management, asset administration and operational and safety administration programs, which may include a risk management program, an engineer program or a project management consulting (PMC) program, among other things.
LNG facilities should be protected against unscheduled shutdowns. There has been a long history of unanticipated LNG plant shut-downs that have been traced back to dangers or flaws that were introduced throughout the different engineering phases—conceptual design, preliminary feasibility studies, full-scale engineering, and construction (EPC). Similar to this, efforts taken to simplify maintenance and operability at the engineering phase have been shown to result in a considerable reduction in the number of unscheduled plant shutdowns. Good engineering techniques and sound equipment design—selection, specification, and cold-eye review—in conformance with codes, standards, and regulations may help to avoid unscheduled shutdowns and maximize uptime. Utilizing sophisticated technology, correct equipment margins, equipment spare/redundancy, numerous trains, enforcing regulations in equipment support structures and related pipes, and using higher-quality construction materials are just a few instances of intrinsically safer design.
Additionally, the success of the project is dependent on the planning and scheduling of all relevant engineering efforts aimed at preventing unexpected shutdowns, such as value engineering, alarm/trip setpoint rationalization, functional safety, risk analysis of equipment failure mechanism, and so on. When developing a new LNG plant, it is generally advisable to begin the program as early as possible, such as during the engineering design phase. All parties involved (engineering contractors, licensors, equipment manufacturers, and so on) should be aware of the owner’s maintenance strategy in order to help prevent unplanned shutdowns. It will also be beneficial to include relevant design requirements in the basis of design to help prevent unplanned shutdowns. The engineer assigned to the owner’s company is normally responsible for verifying that all of these processes are consistent with the owner’s maintenance philosophy.
In order to reduce the likelihood of unexpected shutdowns caused by component wear or equipment failure, it is essential to perform regular maintenance on all key equipment systems during the plant’s operation. However, although the specifics and strategies for executing an advanced maintenance program may vary depending on the maintenance method used, in general, the following stages may be followed:
- Determine the target equipment or systems, including those that are designed with emergency shutdown interlocks, depending on the probable degree of risk associated with a failure.
- Analyze the present state of target equipment or systems using plant monitoring data and inspection data and comparing the results to previous reliability data.
- Set up maintenance priorities in accordance with your needs. It may be necessary to shut down a plant for maintenance and inspection, in which case the scheduled shutdown interval may be re-evaluated based on the potential risk level of major asset equipment in order to reduce the potential risk of failure, maintenance/repair costs, and costs associated with lost production.
Unplanned shutdowns might occur as a result of human mistake from time to time. Despite the fact that a variety of variables may contribute to human error, the use of appropriate corrective measures and best practices can greatly minimize the number of failures attributable to human error that result in unscheduled plant shutdowns. Human error may be minimized during plant operation by extensive training of maintenance employees and field operators, as well as through more in-depth familiarization with the operation and maintenance of different types of equipment in a variety of working settings, for example.