What is a Gasket?
A gasket is a mechanical seal made of deformable material, usually in the form of a ring or sheet, that fills the space between two or more mating surfaces to prevent leakage from or into the joined objects while under compression. Gaskets are essential components in a wide range of industries, including automotive, aerospace, electronics, food processing, petrochemical, and more.
Types of Gaskets in Oil and Gas
In the oil and gas industry, gaskets play a critical role in ensuring the integrity and safety of systems that handle high pressures, extreme temperatures, and potentially hazardous substances. The types of gaskets used in this sector are chosen for their ability to withstand these challenging conditions. Here are the primary types of gaskets commonly used in the oil and gas industry:
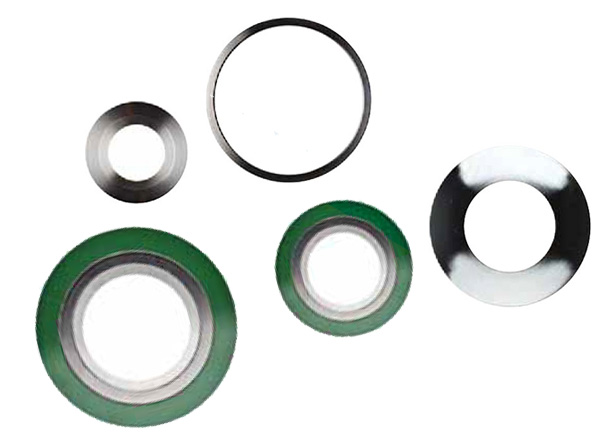
1. Spiral Wound Gaskets (SWG)
Description: Spiral wound gaskets are composed of a mix of metallic and non-metallic materials. They have a spiral-wound construction, typically consisting of a metal strip such as stainless steel and a filler material such as graphite, PTFE, and flexible graphite with metal wire reinforcement.
Advantages: They offer excellent resilience and can maintain a seal under varying pressures and temperatures. Their ability to withstand thermal cycling makes them highly reliable in dynamic environments.
Applications: Due to their resilience and ability to handle high pressure and temperature, SWG gaskets are popular choices for a wide range of oil and gas applications, including flanges, heat exchangers, and pressure vessels. The specific filler material determines their suitability for various fluids and chemicals.
2. Ring Type Joint (RTJ) Gaskets
Description: RTJ gaskets are precision-engineered metal gaskets that fit into machined grooves on flanged connections. They are typically made from high-strength materials such as stainless steel, carbon steel, soft iron, or other alloys.
Advantages: These gaskets provide a very tight, reliable seal and are highly resistant to blowouts, making them suitable for critical service applications.
Applications: RTJ gaskets are widely used in high-pressure applications like pipelines, pressure vessels, and wellheads. Their design provides excellent sealing under extreme pressure and temperature conditions, particularly in upstream oil and gas operations, including wellheads and Christmas trees.
3. Kammprofile Gaskets
Description: These are metallic gaskets with a serrated or grooved profile on one or both sealing surfaces. The serrations create a labyrinthine sealing path, enhancing the gasket’s ability to withstand high pressure. The core material can be metal or a combination of metal and a softer filler material.
Advantages: Kammprofile gaskets offer excellent sealing capabilities and are highly resistant to thermal cycling. They can also be reused after re-layering the soft sealing material.
Applications: These gaskets are used in applications where high performance is needed, such as in pipelines, refineries, petrochemical plants, heat exchangers, boilers, and pressure vessels.
4. Corrugated Metal Gaskets
Description: These gaskets consist of a corrugated metal core, often covered with a soft facing material such as graphite, PTFE, or mica.
Advantages: They provide a good balance between sealing performance and material cost, and their corrugated design enhances flexibility and compressibility.
Applications: Corrugated metal gaskets are used in applications with moderate pressure and temperature, such as flanges in process piping and equipment.
5. Double Jacketed Gaskets (Envelope Gaskets)
Description: Jacketed gaskets feature a soft filler material such as PTFE or elastomer, enclosed in a metallic jacket. The metallic jacket provides strength and corrosion resistance, while the core material offers excellent chemical resistance and sealing properties (it could be graphite, ceramic, or other compressible materials).
Advantages: These gaskets combine the strength and durability of metal with the conformability of the filler material, making them suitable for harsh conditions.
Applications: Jacketed gaskets are used in high-temperature and high-pressure applications. They are ideal for applications involving aggressive chemicals or where high chemical resistance is a priority. They are often used in refineries, chemical processing plants, and offshore oil and gas platforms.
6. Soft Cut Gaskets
Description: Made from non-metallic materials such as graphite, rubber, PTFE, or compressed fiber, soft cut gaskets are cut from sheets into the required shape and size.
Applications: These gaskets are used in low to moderate pressure and temperature applications, such as in pipeline flanges and machinery.
Advantages: They are cost-effective, easy to install, and available in a wide range of materials to suit different media and conditions.
7. Insulating Gaskets
Description: Insulating gaskets are designed to prevent electrical conductivity across a flange joint, helping to prevent corrosion.
Advantages: They protect against galvanic corrosion by electrically isolating different sections of the pipeline. This extends the lifespan of equipment and reduces maintenance costs.
Applications: These are used in pipeline systems where cathodic protection is employed, such as in offshore platforms and underground pipelines.
8. Composite Gaskets
Description: Composite gaskets combine various materials to enhance their properties, such as a combination of metal and soft sealing materials.
Advantages: They offer superior conformability to uneven surfaces, excellent resistance to pressure and temperature extremes, and compatibility with various fluids, allowing for a tailored approach to specific sealing challenges.
Applications: They are used in a range of oil and gas applications, including pipe flanges, valve bonnets, and compressor housings.
9. O-Rings
Description: Although not always considered gaskets, O-rings are circular seals made from elastomeric materials. They are used in static and dynamic sealing applications.
Advantages: They provide an effective seal in a compact form and are available in materials that can withstand a wide range of temperatures and chemicals.
Applications: In the oil and gas industry, O-rings are used in valves, pumps, and hydraulic systems.
10. Non-Asbestos Sheet Material (NASM) Gaskets
Description: NASM gaskets are flat gaskets made from a compressed fiber material with a binder. While traditionally containing asbestos, modern NASM gaskets are asbestos-free and utilize aramid fibers or other high-temperature resistant materials.
Advantages: Compared to traditional asbestos-containing gaskets, NASM gaskets are safer for workers and the environment. They still provide good sealing properties for various applications.
Applications: NASM gaskets are suitable for low to medium-pressure applications involving steam, water, and various oils. They are often used in refineries, pipelines, and other applications where cost-effectiveness is a factor.
Conclusion
The oil and gas industry demands gaskets that can withstand extreme conditions while ensuring the integrity and safety of the systems in which they are used. Selecting the appropriate type of gasket involves considering factors such as pressure, temperature, chemical compatibility, and the specific application. Each type of gasket has its unique advantages and applications, making it essential to choose the right gasket for each specific use case to ensure reliability and efficiency in oil and gas operations.