Overview – METROL SEA-CELL Electrochlorinator
Prevent organism growth in your seawater systems with sodium hypochlorate
Our METROL SEA-CELL electrochlorinator is a machine which helps prevent organism growth in seawater systems. Technically, the electrochlorinator generates sodium hypochlorite by using electricity to control biofilm efficiently. Not only large organisms but also small organisms can be aggregated on the equipment. This would reduce performance and increase lifespan of the system. Therefore, if the seawater is applied in any process, the electrochlorinator should be installed to hinder biofoulant.
The METROL SEA-CELL electrochlorinator offers increased run-times and efficient protection of seawater treatment equipment.
Application
- Offshore: For seawater treatment to use for firewater, cooling, and water injection, and to prevent marine organism growth.
- Oil and gas stations and onboard ships to floating production.
- Storage.
- Offloading (FPSO) facilities.
- Onshore: For water treatment to prevent infestation with fouling organism.
- Industrial and refinery cooling water.
- Common industries: For prevention of blockages in heat exchangers, coolers, and pipework
How it works
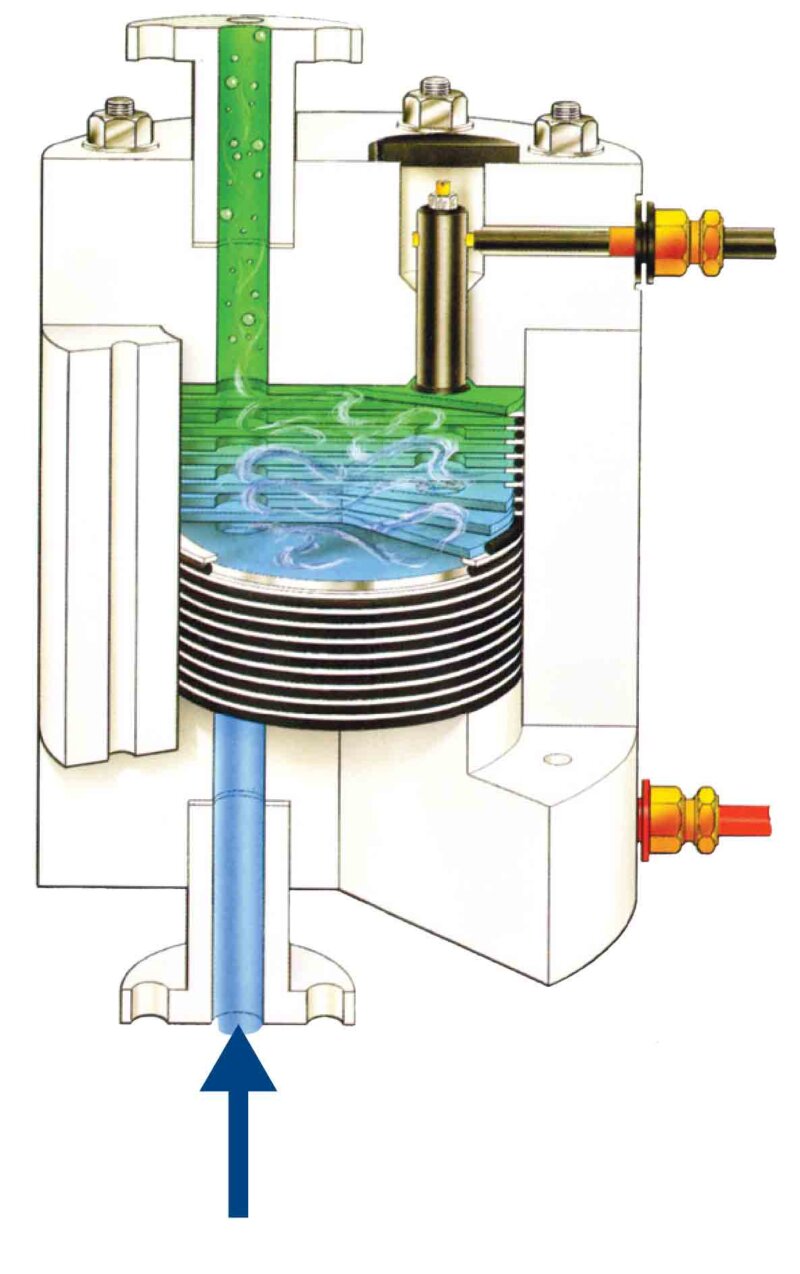
The SEA-CELL electrochlorinator applies “Sodium hypochlorite” via electrolysis as an oxidizing biocide for biofoulant protection.
With reliable design and auto-cleaning generator, our METROL SEA-CELL electrochlorinator has an arrangement which encloses the anode-cathode bipolar plates within a leak-proof, integral housing. Compared to other cell designs, they will use the cathode or anode as the containment device for the process fluid. Since the plates are mounted inside a substantial polypropylene container, the SEA-CELL electrochlorinator can ensure leak-free operation even during anode-cathode failure. The design is guaranteed by ingress protection (IP) 66 rated. Therefore, there is no need for an additional enclosure, and help installation in harsh marine environments.
Due to self-cleaning function, our METROL SEA-CELL electrochlorinator doesn’t need to clean any acid. Instead, the cell plates are kept free of deposits and hydrogen is removed by optimizing fluid velocities.
During the process, the hypochlorite solution is in the tank under level control. After that, it will be pumped to the dosing point where the solution is released to the seawater system by multistage centrifugal dosing pumps.
Hypochlorite generation process
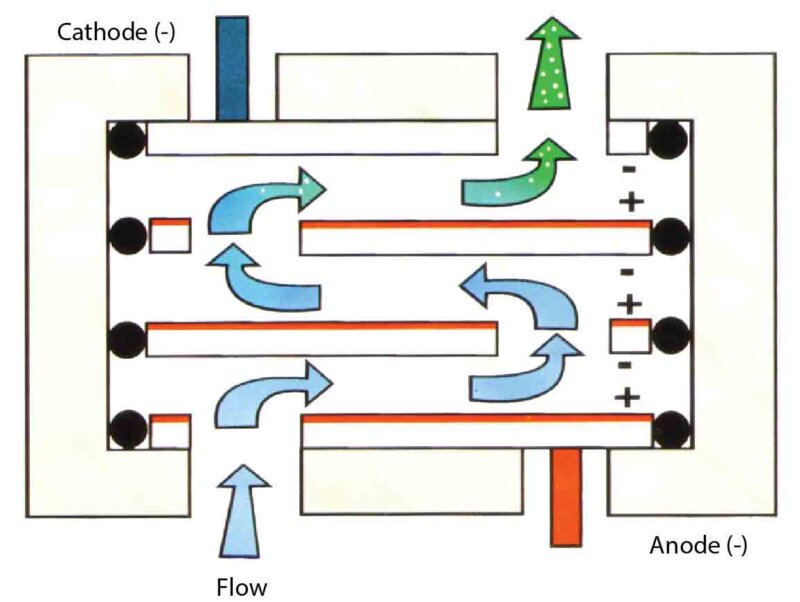
The hypochlorite generation process is involved with electrolysis of the sodium chloride in raw seawater. The solution flows between anodic and cathodic electrodes energized by the direct current. Then, the chemical reactions happen between the products of electrolysis.
Passing direct current through an aqueous solution of sodium chloride causes the chloride ions to migrate to the anode and sodium ions to migrate to the cathode, leading to the generation of chlorine at the anode and hydrogen plus sodium hydroxide at the cathode.
Hydroxyl ions migrate from the cathode area and react with sodium ions and chlorine dissolved in the seawater near the anode to produce sodium hypochlorite
Special Features contain;
- Design to operate at 145 psi [10 bar], pressure tested to 220 psi [15.2 bar], and upto 696 psi [48 bar] during certification trials without leaks
- Compact design reduces weight and space requirements.
- Vertical orientation facilitates removal of hydrogen byproduct of the electrolytic process
- *IP rating of 66; installation in harsh marine environments with no requirements for secondary enclosures
- High-grade titanium electrodes of up to 5-mm thickness for long life and elimination of plate buckling
- Self-cleaning unit and no acid washing
*Remark: Ingress Protection (IP) is an international standard (IEC 60529) used to rate the degree of protection or sealing effectiveness in electrical enclosures against intrusion of objects, water, dust or accidental contact.
Project Reference
- ESSO Sriracha Refinery (EXXON) – 2021
- PTTEP Bangkot Field
Brochure
Download Brochure