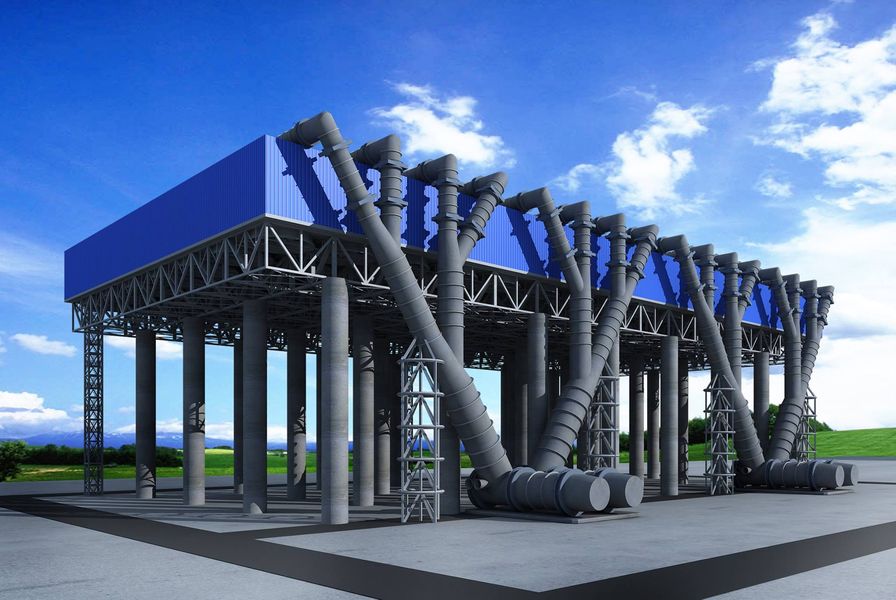
Many facilities are being pushed to convert existing power plants to closed-circuit cooling water systems or even dry cooling alternatives because of escalating environmental restrictions and public pressure, rather than continuing to use once-through river or ocean cooling water. There just isn’t enough water in dry areas to meet the demands of both power plants and people.
Dry cooling may also be adopted early in a project by an astute developer since it broadens plant siting possibilities and may greatly speed up construction permit clearance due to the avoidance of water usage limits. Even a six-month delay in a project’s timeline may have a significant impact on its economics and easily offset the higher capital cost of dry cooling systems.
The Fundamentals of an Air-Cooled Condenser
ACC is a direct dry cooling system that condenses steam within air-cooled finned tubes using vacuum.
The major components of an ACC include ducting (for steam transmission), a finned tube heat exchanger, axial fans, motors, gear boxes, pipelines, and tanks (for condensate collection).
Ambient air is passed through a finned tube heat exchanger with a forced draft axial fan to condense the steam.
The finned tube heat exchanger, which comes in a few forms, is the main component of the ACC:
- SRC (Single Row Condenser)
- MRC (Multi Row Condenser)
The fundamentals of air-cooled condenser design
Direct dry cooling, as opposed to once-through water-cooled facilities, condenses turbine exhaust steam within finned tubes that are externally cooled by ambient air rather than sea or river water. There are two ways to circulate ambient air for condensate cooling: utilize fans to move the air or take use of nature’s draft.
The natural draft system employs the well-known hyperbolic tower, which may reach heights of more than 300 feet and is furnished with a series of heat exchangers. The second, more well-known design option is the air-cooled condenser, which employs motor-driven fans rather than the inherent buoyancy of hot air. Due to the large scale of hyperbolic constructions, natural draft is a specialized usage for tiny areas. As a result, air cooled condensers with mechanical draw are employed in around 90% of the world’s dry-cooled power plants.
The steam from the turbine exhaust enters a steam distribution manifold on the ACC structure’s roof. Following that, the steam is dispersed via fin tube heat exchangers arranged in an A-shape in a “roof structure.” Steam condenses within the tubes due to the cooling action of ambient air pulled across the exterior finned surface of the tubes by the fans. The fans are located at the A-shape structure’s base. Condensate drains from fin tube heat exchangers into condensate manifolds and subsequently to a condensate tank before being directed to the boiler or standard feed heating system.
An Air Cooled Condenser works in the same way as a regular surface condenser under vacuum. Air and other non-condensable gases enter the steam through a variety of routes, including system border leaks and the steam turbine. Non-condensable gases are evacuated in the Air Cooled Condenser ‘s “secondary” section, which is connected to vacuum pumps or air ejectors that exhaust the non-condensable gases to the atmosphere.
The heat exchanger and its finned tubes are the primary distinction between
The heat exchanger and its finned tubes are the primary distinction between
The heat exchanger and its finned tubes are the primary distinction between
The heat exchanger and its finned tubes are the primary distinction between Air Cooled Condenser systems from various manufacturers. There are two kinds of heat exchangers: single-row and multi-row. There are various arguments for and against each idea’s benefits. The single-row construction is clearly advantageous in very cold circumstances. In addition, the market offers three tube shapes: round, oval, and flat. The most advanced tubes are spherical and flat, and they function well in almost all situations.
systems from various manufacturers. There are two kinds of heat exchangers: single-row and multi-row. There are various arguments for and against each idea’s benefits. The single-row construction is clearly advantageous in very cold circumstances. In addition, the market offers three tube shapes: round, oval, and flat. The most advanced tubes are spherical and flat, and they function well in almost all situations.
systems from various manufacturers. There are two kinds of heat exchangers: single-row and multi-row. There are various arguments for and against each idea’s benefits. The single-row construction is clearly advantageous in very cold circumstances. In addition, the market offers three tube shapes: round, oval, and flat. The most advanced tubes are spherical and flat, and they function well in almost all situations.
systems from various manufacturers. There are two kinds of heat exchangers: single-row and multi-row. There are various arguments for and against each idea’s benefits. The single-row construction is clearly advantageous in very cold circumstances. In addition, the market offers three tube shapes: round, oval, and flat. The most advanced tubes are spherical and flat, and they function well in almost all situations.
Suppliers differ in terms of fin form as well. Under transitional situations, some fin designs are less prone to fouling and mechanically more durable. Fins of the highest quality are tightly connected to the bare tube, resulting in a useful life expectancy equivalent to that of power plants.
The material used for the finned tubes is the last crucial design element. The two most dependable power plant technologies are aluminum fins brazed on flat bare aluminum tubes wrapped in aluminum or oval galvanized finned tube bundles.
If Air Cooled Condenser is chosen, a plant site in China, as well as other areas worldwide, is not necessary to be near a water supply. Instead of transmission lines, either gas distribution lines (for combined-cycle facilities) or rail lines might be optimized (for coal-fired plants). China’s solid fuel facilities are often located near coal mines, which explains why the government is now interested in air cooling. Finally, land expenses may be decreased if a lake, river, or coastal plant site is not necessary.
Market for Air Cooled Condensers
Europe had a tiny market for big or medium-sized power plants between the 1960s and the 1990s. Instead, it relied on massive coal-fired power facilities and nuclear reactors. Dry-cooling designs, on the other hand, have grown in favor because of water scarcity in the Middle East, China, South Africa, and the United States (at coal mine locations, in desert environs, or for other similar reasons). After 1990, the global market for dry cooling started to develop, and it has more than doubled in the last 13 years.
The market for dry-cooling equipment is projected to stay busy soon, owing to China’s enormous electrical demand. Reasonable increase is also anticipated in Europe, as several European Union member nations reaffirm their commitment to manage future water resources. In the foreseeable future, the Middle East (Emirate’s region) and India will undoubtedly become two enormously significant markets. Since the middle of 2005, the market in the United States has been progressively expanding.