Natural gas is mostly composed of methane (often at least 90%), although it may also include ethane, propane, and heavier hydrocarbons. The “pipeline” of natural gas may also include trace quantities of nitrogen, oxygen, carbon dioxide, sulfur compounds, and water. During the pre-treatment process, oxygen, carbon dioxide, sulfur compounds, and water are all removed.
The liquefaction process compresses, cools, condenses, and reduces the pressure and temperature at which methane, the principal component of natural gas, liquefies. The whole process may be adjusted to produce the purest form of LNG.
Storage and regasification of LNG Cylinder
By storing LNG and providing natural gas to final users, LNG receiving terminals contribute to the LNG value chain. A pipeline, LNG storage tanks, compressors, vaporizers, pumps, and other components are often included. The LNG from the LNG carrier ship is transferred to the storage tank through the unloading pipeline. The stored LNG is transported to the vaporizer process by a pump in the storage tank. The vaporization process is used to provide natural gas to the end user.
Recirculation, depressurization, and unloading are all steps in the LNG unloading process. To prevent pipeline heat prior to LNG unloading, the unloading pipeline must be kept cryogenic. A little amount of LNG from the storage tank is continually cycled through the pipeline during the recirculation stage to keep it cool. The pipeline pressure is decreased to the amount necessary to carry LNG from the carrier to the storage tank during the depressurization process. Following the unloading stage, the process advances to the first phase of recirculation.
The vapor from the LNG constantly evaporates due to the absorbed heat in the storage tank and the cryogenic pipelines during the unloading and storage of LNG Cylinder. This vapor is referred to as boil-off gas (BOG). Because of the 600-fold increase in volume, it may cause physical damage in LNG facilities. When the BOG is over-treated, more energy is used. As a consequence, effective BOG management is required for energy savings. For LNG receiving facilities, re-condensation and direct compression are popular BOG handling processes. Using a BOG compressor, BOG from the storage tank is compressed to roughly 10 bars and blended with enough send-out LNG to generate a liquid mixture, which is then pumped into the re-condenser. The liquid combination is compressed to supply pressure and evaporated by saltwater in a high-pressure (HP) pump. The BOG will not be condensed in the re-condenser if the LNG rate indicated in the requests is insufficient to condense all of it. The HP compressor compresses the residual BOG in the re-condenser to pipeline pressure and instantly delivers it to the pipeline, where it is mixed with the natural gas (Park et al., 2010). Because the HP compressor uses a substantial amount of energy, it is desirable to decrease the HP compressor’s operation.
Refrigeration of LNG Cylinder
No amount of insulation, no matter how efficient, can keep the temperature of LNG cold on its own. LNG is stored as a “boiling cryogen,” which implies that at its boiling point at the pressure at which it is stored, it is a very cold liquid. The temperature of stored LNG Cylinder is comparable to that of boiling water, but 470°F [243°C] lower. The temperature of boiling water (212°F [100°C]) does not change with increasing heat because it is cooled by evaporation (steam generation). Similarly, if kept at constant pressure, LNG will keep its temperature close to constant. This is referred to as “auto refrigeration.” As long as the steam (LNG vapor boil off in LNG Cylinder) is allowed to depart the tea kettle, the temperature will remain constant (tank).
If the vapor is not removed, the pressure and temperature inside the vessel will rise. Even at 100 psig [6.7 barg], the temperature of the LNG will be about -200°F [-129°C].
LNG Cylinder of Vehicle Fuel
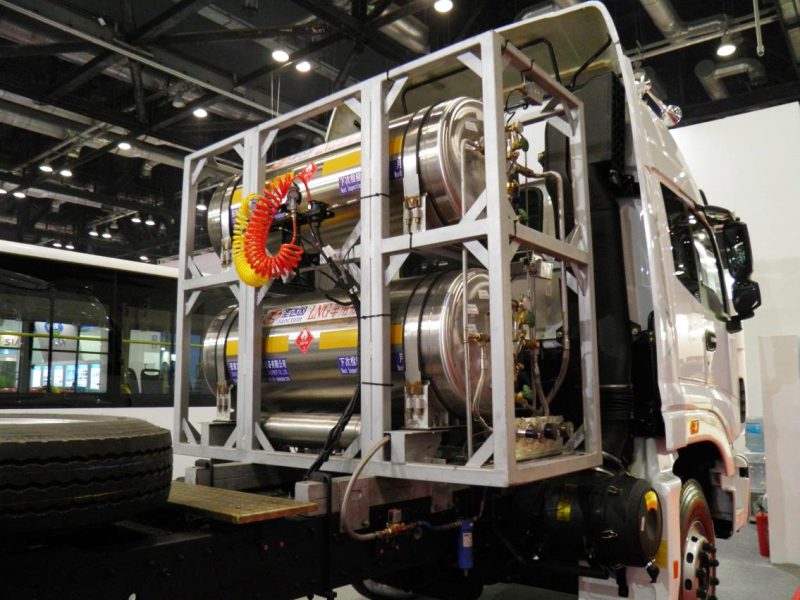
The vehicle cylinder is a vacuum super insulated cryogenic container that allows liquid natural gas to be stored at low temperatures for lengthy periods of time with very little usage.
- Make safety your first concern. Only manufacture LNG cylinders that pass the inspection items outlined in the Codes and Standards.
- Extremely long service life Using acquired expertise and know-how, manufacture cryogenic liquefied gas cylinders for industrial applications.
- Superior thermal insulation 90 percent insulation technology that does not bend even after being completely charged for 5 days
- A straightforward repair structures
- Plan for easy component replacement in the case of a problem.
- Customized production based on customer specifications We have superior LNG cylinder design and manufacturing methods that enable us to respond swiftly to demands regardless of vehicle type or volume.
As we can see, LNG storage system is working on the very low range of temperature, or on the cryogenic process. It is important and mandatory that to operate in the low region temperature, the materials and process have to withstand the cryogenic effect. This causes the cryogenic tanks to be considered as one of the main component and important equipment for LNG Storage System as well.